With the rapid development of modern science and technology and industrial fields, pipe parts are playing an increasingly important role in various industries such as engineering machinery, transportation, agricultural and animal husbandry machinery, kitchen utensils, and fitness. At the same time, with the emergence and rapid development of CNC laser pipe cutting machines, laser cutting pipes have unique features such as narrow incision width, small thermal impact, fast cutting speed, clean incision, good flexibility, and the ability to adapt to the shape and type of the pipe being cut. There are many advantages such as no obvious restrictions on thickness, thickness, etc., which make the advantages of laser cutting pipe technology more prominent than traditional pipe processing methods. Laser pipe cutting technology can improve the quality of cutting processing, ensure processing efficiency, simplify the processing process, and also greatly improve the economic benefits of the majority of laser pipe cutting users. However, laser cutting pipes is a complex process, and there are many factors that affect the cutting effect. We need to analyze the problems that arise during the cutting process, and then find certain methods to solve them.
Inability to cut through or the incision is not smooth
There are four main reasons why the cut cannot be cut through or the cut is not smooth during laser cutting.
Cutting speed too fast
Especially when cutting special pipes or high-thickness pipes, such as profiles, special-shaped pipes, etc., when the cutting head cuts to the corner, because the thickness of the corner becomes larger and the cutting speed is too fast, it is easy to fail to cut through or the cut is not smooth. ,As shown in Figure 1. In this case, the cutting speed is generally reduced at the cutting corner and the pressure of the auxiliary gas is increased.
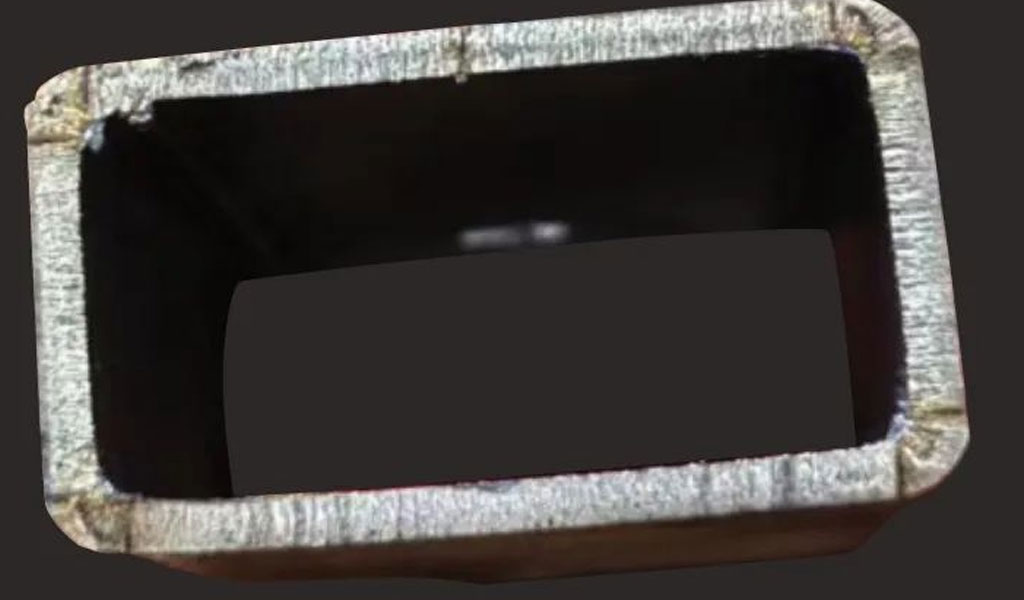
The focal length of the cutting head is improperly adjusted or the laser light path of the cutting head is incorrect.
The focal length of the cutting head will also affect the cutting quality of the pipe. The normal focus of the cutting head has three states: negative focus, zero focus, and positive focus. Among them, positive focus cutting is suitable for oxygen cutting of carbon steel materials, and zero focus is suitable for cutting thin plates. , negative focus is suitable for nitrogen/air cutting of stainless steel, carbon steel, galvanized steel, aluminum, copper and other materials, which requires us to choose the correct focus position of the cutting head when cutting different pipe materials.
The incorrect optical path of the cutting head will also have a great impact on pipe cutting. Therefore, during trial cutting, the spot position of the cutting head must be constantly adjusted so that it can produce a very round spot on the laser test paper.
The cutting head protection lens and focusing lens are contaminated, and the water source of the cooling system is not clean.
When the cutting head is cutting normally, the auxiliary gas is continuously cooled and removed. However, due to the high temperature during cutting, the protective mirror and focusing lens of the cutting head will still be easily contaminated. As shown in Figure 2, once the protective mirror or focusing lens of the cutting head is If the focusing lens is contaminated, it will cause the pipe to be cut through or unable to be cut.
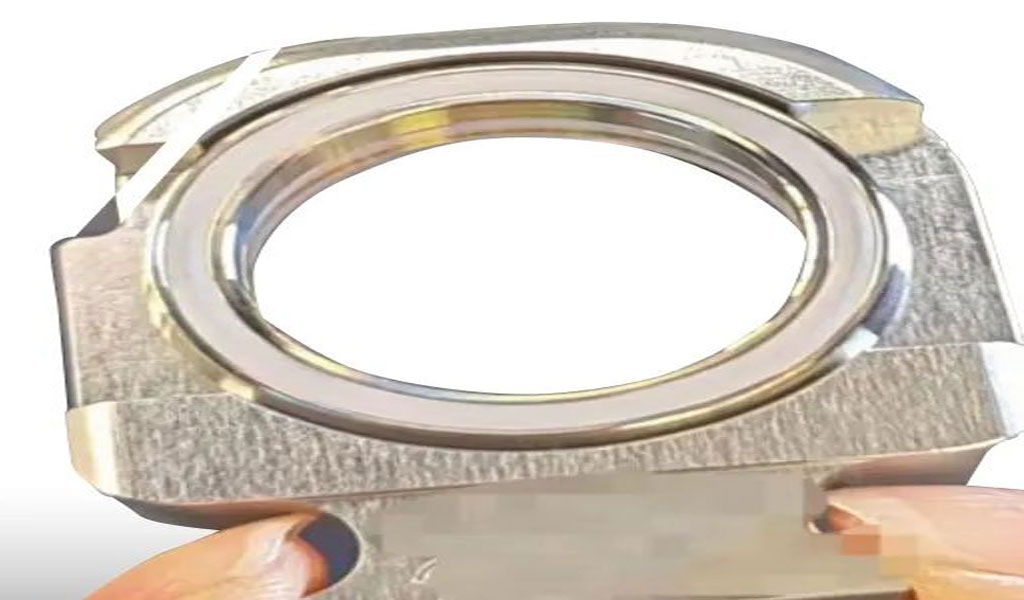
If the laser cutting system uses unclean water, it will at least affect the cooling effect of the entire cutting system, cause the cutting head and generator waterways to be blocked, affect the pipe cutting quality, and at worst, cause damage to the generator and cutting head, leading to greater economic losses. , so the laser cutting system must use pure water, preferably distilled water, to avoid waterway blockage in the cutting head and generator that affects the cooling effect.
The laser output power is too large or the cutting head nozzle is improperly selected.
When laser cutting pipes with symmetrical surfaces such as round tubes and square tubes, due to the excessive laser output power, usually after cutting off the front side of the cutting surface, a melted edge will appear at the edge of the cutting seam, and the molten slag will fall along the cutting seam. The inside of the symmetry plane is equivalent to adding a layer of thickness to the inside of the pipe. When the cutting head cuts the symmetry plane, the slag will fall at the previous cutting seam, causing the entire pipe to be cut continuously; even if it has been cut, the cut surface It will also be quite rough, affecting the overall pipe cutting quality. Therefore, before cutting, it is necessary to conduct perforation and trial cutting tests to test the optimal laser output power and auxiliary gas pressure.
The nozzle selection of the cutting head will also have an impact on the cutting quality. Generally, the dual-jet nozzle is suitable for fine-cut pipes and is mainly used for cutting pipes with small thickness, high precision and fast speed, while the single-jet nozzle is suitable for pipes with large thickness. , cutting pipes with complex materials and low precision requirements. Therefore, during trial cutting, selecting a cutting head nozzle suitable for the current pipe can ensure the overall cutting quality of the pipe and improve cutting efficiency. The nozzles of single-jet and double-jet cutting heads are shown in Figure 3.
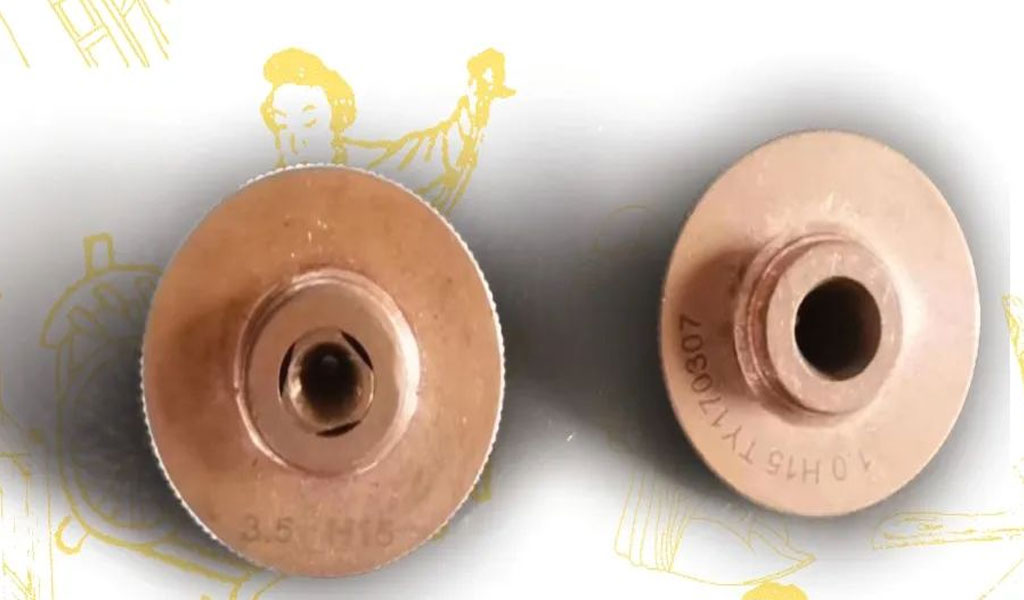
The cutting start line and the end line do not coincide or the cutting pattern does not meet the requirements.
“Pipe laser cutting” is mainly used to cut various hollow circular pipe materials of non-metallic solid materials, such as plastic pipes, PVC pipes, PVB pipes and other industrial and civilian materials. This kind of pipe is generally used in home decoration, industry, and water conservancy construction. This laser machine uses a CO2 metal laser tube and consumes about 100W-500W of power. It is the preferred processing machine for small and medium-sized enterprises.
The parameter settings of each axis of the machine tool are inaccurate
Generally, the laser pipe cutting machine is composed of several basic control axes such as X-axis guide rack transmission, Y-axis guide screw transmission, Z-axis cutting head cutting, and W-axis clamping and feeding chuck rotation. When setting the parameters of each axis of the machine tool, any error in the gear tip circle size, guide rail screw lead, cutting head screw lead, and W-axis gear transmission ratio will have a great impact on the final cutting effect. Some even affect the good operating status of the entire laser pipe cutting machine. Therefore, after turning on the machine tool, first check whether the setting parameters of each axis are correct, and then put the machine tool into work.
The X axis of the machine tool is not perpendicular to the Y axis or the Z axis is not perpendicular to the X axis
When the X-axis and Y-axis of the laser pipe cutting machine are not perpendicular, the circular pattern cut on the pipe surface will be out of round. As shown in Figure 4, the cut square pattern will become a parallelogram; when Z When the axis is not perpendicular to the One of the reasons for continuous cutting of pipes. Therefore, when cutting pipes, if the above phenomenon is found, use a dial indicator to calibrate it as soon as possible. At the same time, you can check whether the mounting screws of the guide rail, rack, and screw are loose, and whether the gears are worn.
Conclusion
As the status of laser cutting pipes in the entire laser cutting industry is getting higher and higher, especially the laser pipe cutting machine has gone through a series of development processes from manual cutting to semi-automatic cutting to semi-assisted cutting to fully automatic cutting. More and more people are using it. People have discovered the huge potential of laser pipe cutting machines in the field of production and processing. This requires us to be able to discover various problems that arise in laser cutting of pipes while using laser pipe cutting machines, so as to propose improvement measures for these problems, continuously improve the laser cutting system and laser cutting process, and further promote laser pipe cutting. The machine is developing in the direction of high speed, high precision, high automation, flexibility and diversified functions, which is of extremely important significance to the rapid development of the entire laser cutting industry.